Fabricare Canada – HLS: A Laundry is Energized!
Let’s go back four years. At Ottawa’s Hospital Linen Services changes were needed. The technology was old, efficiency was poor, employee morale was low, what’s more customers were unhappy with the quality and service they were receiving. If ever there was a need for a legendary ‘caped crusader’, this was it.
The first surprise is that such an individual was near at hand, working as the chief financial officer for the corporation. The second surprise is that the Board of Directors endorsed and backed him to take over the job of manager, and ultimately CEO of the laundry – a position for which he had no training. And the third surprise is that this lack of knowledge proved to be one of the keys to a dramatic turnaround at Hospital Linen Services.
One of the other keys was the personality and drive of the new CEO, Rocco Romeo, who has galvanized the work force and improved the technology in this 100,000-sq.-ft. plant, which processes 23,000,000 lbs of linen a year. Here’s how he went about it.
One Department at a Time
He learned the operation by spending time in each department, starting with the flatwork ironers. First he asked the people working there what they were doing and how their department fit into the total processing in the plant. Then, without any pre-conceived notions or engineering studies, he went through the movements of staff and the functioning of the equipment involved. Being an outsider he was able to spot inefficiencies, duplication of efforts and ways to improve workflow and quality.
He had the advantage of an experienced assistant in Pete Rainville, now operations manager, who was able to implement changes or point out other options. The pair worked through the plant, including its five Lavatec tunnel washers and four flatwork ironers, and an OR pack department with 27 people, to say nothing of folding, assem- bly and shipping operations. Each department became aware of its importance to the whole and began to take pride in improving quality. “Show people that you care, or they don’t care,” commented Rocco.
Meeting with Customers
It was one thing to improve efficiency, but input from customers was necessary to show where service needed to be improved. Along with customer service manager Gail Dufresne, Rocco had meetings with linen users, OR staff and representatives from the long- term care facilities served by the laundry.
Here he learned that his facility had lost credibility with its customers. They were receiving poorly washed, poorly pressed linen and, in addition, they were not receiving the correct amount of linen for their requirements. The OR departments described the dissatisfaction of surgeons over the packs and pointed out that when surgeons are unhappy, every- one is unhappy.
Getting to Work
What followed this ground- work was four years of not only physical work, but confidence-building. Staff realized they were not being criticized, but being given the tools to do a better job. This re-energized everyone, allowing them to focus on the needs of the customer. New ideas and suggestions were encouraged and staff was made to feel ownership for what they were doing – even to the extent of having pieces of equipment painted with the nicknames they gave them.
In his quest to improve washing quality, Rocco consulted his fellow members of IATHM, the International Association for Healthcare Textile Managers. Through them he learned of a wash- room technology supplier from the U.S., Gurtler Indus- tries. He challenged Alan Gordon, vice-president of corporate accounts, to improve the overall quality of his wash, cut the re-wash rate and pre- serve colours. The major elements Gordon and technician Guy Seguin were working with were four 6-compartment tunnel washers and one 10-compartment washer. Gurtler was able to solve his washing problems and Hospital Linen Services became Gurtler’s first Canadian customer.
Changes in or Packs
The most crucial items being shipped from a hospital laundry are the operating room packs. These are inspected and assembled in a special Clean Room. The organization, as well as the quality, of the packs is strictly controlled. As Rocco described it, a complete culture change was necessary for the 27 people work- ing in this department. Their dedication to quality had to be absolute in preparing the 10,000 packs shipped each week.
Also, changes were made in the content of the packs. Many disposable items were replaced with reusable textile ones. This move to reusables improved quality and, ultimately, saved money. The reusables more than paid for themselves in their service life, and the cost of disposing of disposables was reduced.
A vital portion of the OR pack is the ability of the barrier cloths (used for draping) to resist any moisture. One of the biggest problems experienced in OR was spotting by mineral oil, which can destroy the integrity of the cloth. Gurtler’s Post Shield washing product was able to prevent this penetration. Each barrier cloth is barcoded to keep track of its launderings. When the count reaches 50, and every 10 launderings after that, the cloth is tested with alcohol to check its ability to resist oil penetration.
Barcodes, Barcodes Everywhere
All linen is barcoded. In the case of missing scrub suits, after three months in which the barcode reader has not recorded a laundering, the client is billed for them. Each facility, working with CSM Gail Dufresne, sets up stand- ing orders. These can be changed as needed, but the barcode enables the plant to control shipments and be sure no customer is shorted in delivery.
The Bottom Line
If you want to see lots of smiles, just walk through the Hospital Linen Service plant today. You will meet many of the 150 people who work there, and see their pride in what they do. They know the plant has a 35% increase in pieces per operator hour. They know that not only are their long-time customers pleased with the linen they are receiving, but that new customers are attracted to the facility. They also know that within a few years they will be moving into a 200,000-sq.-ft. facility to house the laundry.
Through their hard work and cooperation, the laundry has been turned around. It has acquired new equipment, new systems and is now working on ISO 9001 certification. But it hasn’t all been work. In the past year there was a fajita party, prepared by Rocco and Pete, and a big 30th anniversary celebration and barbecue. Yet even while taking the official anniversary photos, the reason behind the celebration was not forgotten. Proudly displayed in the foreground of each picture was an assortment of the linens produced by the plant.
Fabricare Canada intends to follow the further achievements of the caped crusader Rocco Romeo and his indispensable assistants Pete Rainville and Gail Dufresne, as they continue the saga of Hospital Linen Services.
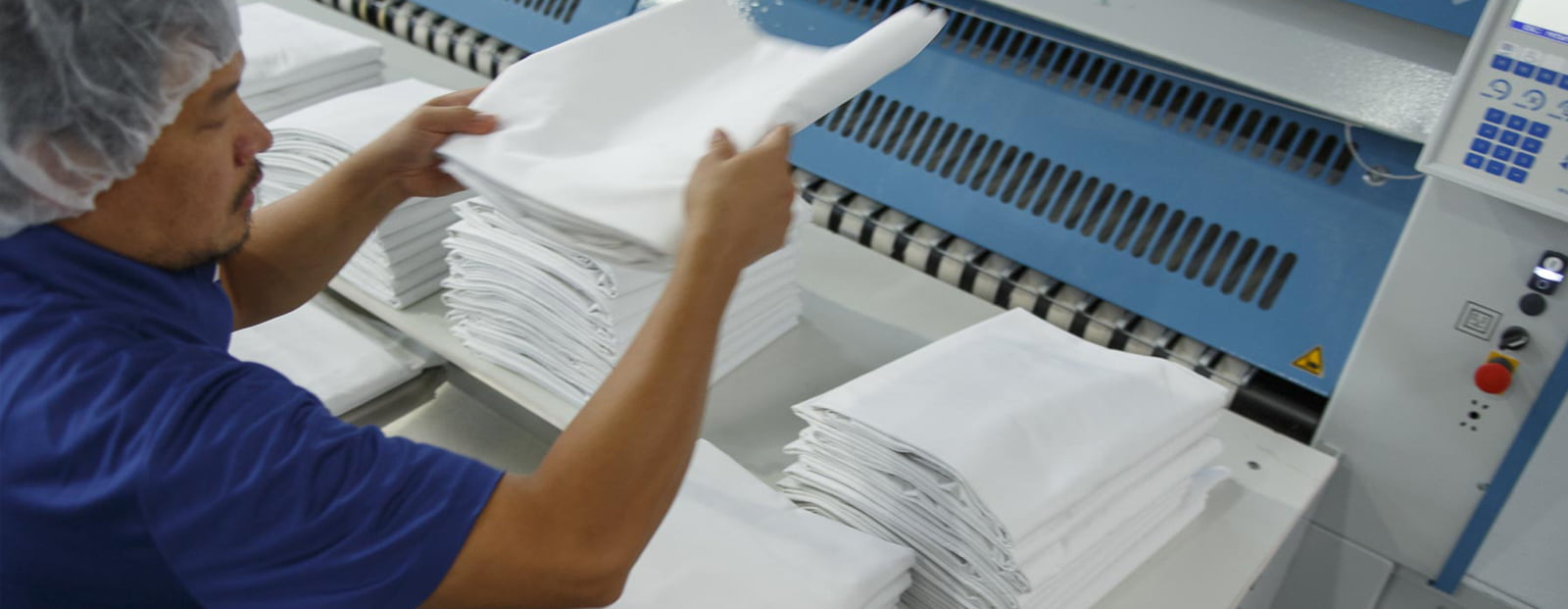